Application of Vision Inspection in Food Packaging
Shreyas Rao
12/5/20245 min read
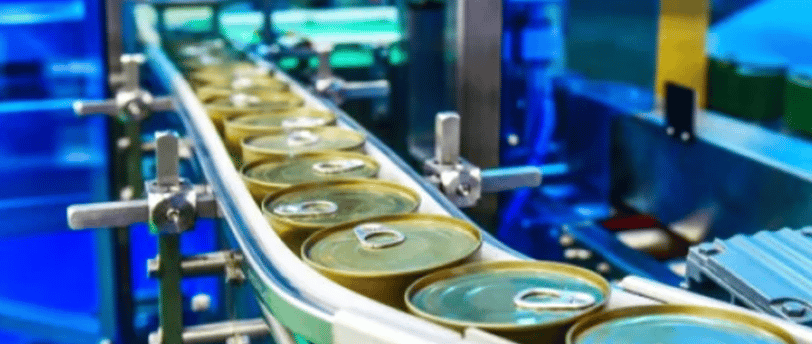
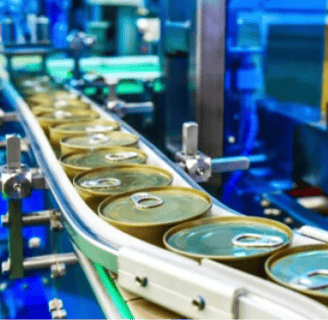
In the fast-moving consumer goods (FMCG) sector, quality control is crucial—especially when it comes to food products. Food packaging not only preserves the product but also ensures consumer safety, maintains freshness, and builds trust in the brand. Tin containers are widely used for food packaging, particularly for products like canned vegetables, fruits, meats, soups, and beverages. However, ensuring the integrity and safety of food packed in tin containers can be challenging due to the need for precise sealing, proper labeling, and contamination prevention.
This is where vision inspection systems come into play. Equipped with high-resolution cameras and advanced image processing software, these systems automate the inspection process, allowing for non-contact, real-time quality checks. In this blog, we will explore the key use-cases for vision systems in tin food packaging and highlight the numerous benefits they offer food manufacturers.
Key Use-Cases of Vision Systems in Tin Food Packaging Inspection
Seal and Lid Integrity Inspection The integrity of the seals and lids on tin containers is critical for preserving the food inside. A compromised seal can lead to contamination, spoilage, and even dangerous situations, like leakage. Vision systems play a vital role in inspecting seals to ensure they are tightly sealed, properly aligned, and free from defects such as dents or deformations.
Using high-resolution imaging, vision systems can detect imperfections in real-time, allowing for immediate corrections on the production line. This reduces the risk of spoiled products reaching consumers and ensures long shelf life by maintaining an airtight seal on the containers.
Fill Level and Content Verification Accurate fill levels are essential in ensuring the right quantity of food in every tin container. Both underfilling and overfilling can lead to consumer dissatisfaction, wastage, and inefficiency. Vision inspection systems can precisely measure the fill levels of each container, ensuring that they meet the required standards.
These systems also provide quick detection of discrepancies, ensuring consistency across large production batches. By automating the fill level verification process, manufacturers can reduce the chances of human error, enhance efficiency, and maintain uniformity across the entire product range.
Label and Print Quality Inspection Labels on tin food containers provide essential information, including product name, ingredients, nutritional details, and expiration dates. Accurate labeling is not just important for compliance with food safety regulations but also for consumer trust and brand integrity. Vision systems are highly effective at inspecting the label placement, print quality, and legibility.
These systems can detect misprints, faded text, incorrect product details, or label misalignment, ensuring that all products meet the highest standards. This reduces the chances of misbranding, incorrect information, or regulatory non-compliance, safeguarding both the consumer and the brand.
Container Shape and Geometry Inspection Tin containers need to maintain a consistent shape to fit properly on shelves, in transport, and within automated packaging systems. Any deformation, such as dents, scratches, or warping, can compromise both the aesthetic and functional qualities of the package.
Vision systems inspect the geometry of each tin container to detect any shape distortion. This includes evaluating the roundness, symmetry, and integrity of the tin. By catching defects early, manufacturers can prevent flawed containers from progressing to later stages of production, thus improving product quality and operational efficiency.
Foreign Object Detection Foreign object contamination is a significant concern in food packaging, where even small particles like metal shards, plastic, or glass can lead to food safety risks. Vision systems equipped with advanced imaging capabilities can detect such foreign objects inside or outside the tin containers, ensuring the final product is safe for consumption.
High-definition cameras, paired with specialized software algorithms, can identify even the smallest contaminants in the tin containers. This proactive inspection not only ensures consumer safety but also helps manufacturers meet stringent food safety standards and avoid costly product recalls.
Date and Batch Code Verification Expiration dates and batch codes are vital for traceability, inventory management, and consumer safety. Misprints or missing codes on tin containers can lead to regulatory violations, consumer confusion, and safety concerns. Vision inspection systems automatically verify that all printed dates, batch codes, and other critical information are correctly placed and legible.
Automated date and code verification ensures that every tin container is compliant with industry standards and ready for distribution. This traceability feature also makes it easier for manufacturers to manage stock, perform recalls if necessary, and maintain full transparency.
Key Benefits of Vision Systems in Tin Food Packaging
Improved Product Safety and Quality Control The primary benefit of vision inspection systems is their ability to improve food safety and quality control. By automating the inspection of tin containers, manufacturers can ensure that every package meets the highest standards. This includes verifying proper sealing, ensuring correct fill levels, detecting label errors, and preventing foreign object contamination.
The ability to detect defects early in the production process reduces the chances of defective products reaching the market, enhancing both food safety and overall product quality. By maintaining consistent packaging quality, manufacturers can also boost consumer confidence in their products.
Non-Contact, High-Speed Inspection Vision systems offer a significant advantage over traditional methods by providing non-contact inspections. Since the system relies on cameras and imaging software rather than physical touch, there is no risk of contamination, damage, or alteration to the food or packaging. This is especially important in food manufacturing, where cleanliness and integrity are critical.
Furthermore, these systems are designed for high-speed operations, allowing for fast inspections without slowing down the production process. In fast-paced manufacturing environments, like food canning, speed and accuracy are vital for meeting production quotas and maintaining product consistency.
Cost Efficiency and Waste Reduction By identifying packaging defects, underfilled containers, or incorrect labeling before they leave the production line, vision systems help reduce waste and rework. This results in substantial cost savings, as manufacturers do not need to discard or reprocess defective products further down the line.
Additionally, vision inspection systems ensure that each container is filled to the correct level, preventing material wastage and enhancing resource efficiency. The ability to quickly spot and address issues minimizes downtime and optimizes production cycles.
Enhanced Compliance and Traceability Food manufacturers must comply with a wide range of industry regulations, including labeling standards, food safety requirements, and traceability mandates. Vision systems help ensure compliance by providing a detailed record of each inspection, which can be used for audits and regulatory inspections. This data ensures that every batch of food is traceable from production to distribution.
With automated date and batch code verification, vision systems support better inventory control and product traceability, making it easier for manufacturers to meet compliance requirements and avoid penalties.
Increased Operational Efficiency Manual inspections can be time-consuming and prone to human error, leading to inefficiencies and inconsistent results. Vision systems streamline the inspection process by automating tasks such as seal verification, label checks, and fill level measurements. This leads to faster production cycles and a more efficient use of resources.
Additionally, the automated nature of these systems allows manufacturers to reduce the need for labor-intensive quality control processes, freeing up resources to focus on other areas of production. Vision systems also provide real-time feedback to operators, allowing for quick corrective actions when needed.
Improved Brand Reputation and Consumer Confidence In the highly competitive food industry, a strong brand reputation is invaluable. Consumers expect the highest standards of quality and safety from food products, especially in canned goods, where packaging plays a significant role in product protection. By ensuring consistent, high-quality packaging, vision systems help food manufacturers maintain brand integrity.
With automated quality control, manufacturers can prevent issues such as misprints, contamination, or packaging defects from reaching consumers, which ultimately improves consumer trust in the brand. By investing in advanced technology like vision inspection systems, manufacturers can demonstrate their commitment to product quality and safety, fostering long-term consumer loyalty.
Conclusion
Vision inspection systems are revolutionizing the food packaging process in the FMCG sector, particularly for tin containers. These systems enhance food safety, improve packaging quality, and ensure regulatory compliance by automating key inspection tasks such as seal integrity, fill levels, labeling, and foreign object detection. The ability to conduct non-contact, high-speed inspections reduces costs, minimizes waste, and enhances operational efficiency.
As the demand for safe, high-quality, and consistently packaged food continues to grow, vision systems will remain an indispensable tool for manufacturers striving to meet consumer expectations and industry standards. By adopting these advanced technologies, food manufacturers can ensure the production of safe, reliable products that consumers can trust.
For more information on how vision inspection systems can benefit your shopfloor, contact us today at info@factree.ai
Industries
© 2024. All rights reserved.