Artificial Intelligence for Bottle Inspection
Shreyas Rao
3 min read
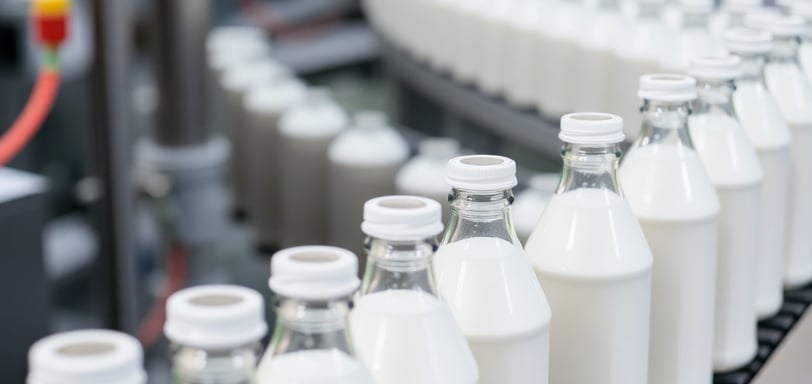
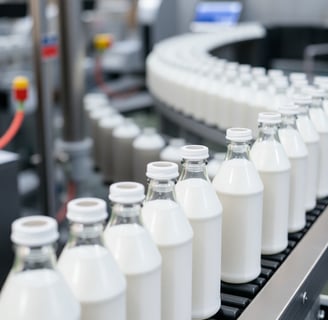
In the modern packaging industry, plastic bottles are one of the most widely used forms of packaging due to their versatility, light weight, and cost-effectiveness. However, ensuring the quality and consistency of plastic bottles during production can be challenging. Even minor defects can lead to significant problems, including damaging product integrity, customer dissatisfaction, and increased production costs. Fortunately, AI-based vision inspection systems are proving to be an effective solution for identifying and eliminating defects in plastic bottles, ensuring high-quality production and reducing the risk of errors.
Common Defects in Plastic Bottles:
Surface Scratches and Marks : Scratches, marks, and abrasions on the surface of plastic bottles can result from contact with moving parts, poor handling, inadequate tooling. These imperfections can affect the aesthetic appeal of the bottle and may even interfere with label adhesion.
Uneven Wall Thickness : Variations in wall thickness can lead to instability and potential breakage. Bottles with inconsistent wall thickness are often the result of faulty blow molding equipment or poor material distribution.
Deformation/Ovality : Bottles can become deformed during manufacturing or post-production processes, such as cooling or handling. Deformation may lead to poor stacking, difficulty in filling, and issues with sealing.
Foreign Contaminants : Plastic bottles may become contaminated with dust, unmelted particles, or other foreign objects during production.These contaminants can be harmful to both the quality of the product and the consumer experience.
Discolouration : Color inconsistencies or discolouration can occur due to inconsistent material blending or incorrect additives. Such defects affect the visual appeal of the bottles and may signal potential issues with the production process.
Lip Cut : Incorrect adjustments of the lost neck cutter or temperature variations in the blade can result in lip cut errors. Improper lip cut can result in sealing issues of the finished goods.
Flow Lines : Streaks/Lines/patterns on the surface of the bottle that differ in colour which typically is caused due to material accumulation in the parision.
Orange Peel : Rough uneven dimpled surface due to mold sweating or condensation.
How AI-Based Vision Inspection Systems Solve These Problems?
AI-based vision inspection systems use advanced computer vision algorithms and machine learning to detect, classify, and measure defects with high accuracy in real time. Here's how these systems can help solve the plastic bottle defect problem:
Automated Defect Detection: AI-powered systems can scan each plastic bottle during production for defects such as thin walls, scratches, and deformities. Unlike traditional manual inspection methods, AI systems can process high volumes of bottles quickly and accurately, identifying even the smallest defects that may go unnoticed by human inspectors. Often the best of the humans are only 85-90% accurate.
Real-Time Quality Control : Vision inspection systems integrated with AI can operate in real-time, providing immediate feedback to operators about production anomalies. This allows for quick corrective actions, minimising downtime and reducing waste.
Improved Consistency and Precision : AI-based systems are programmed to recognise specific patterns and anomalies, ensuring that no defective bottle slips through the production line. These systems continuously learn from historical data, improving their detection accuracy over time.
Reduction in False Positives : With the use of machine learning, AI inspection systems can reduce the number of false positives (incorrectly identifying a bottle as defective) by better distinguishing between genuine defects and normal variations in the manufacturing process.
Enhanced Productivity : Automated AI vision inspection significantly reduces the need for manual inspection, leading to faster production cycles, reduced labor costs, and the ability to process more units in less time without compromising quality.
Traceability and Reporting : AI systems can provide detailed reports on defect trends, allowing manufacturers to identify the root causes of recurring issues and implement long-term solutions. This traceability ensures a consistent level of product quality and helps with compliance to industry standards.
Cost Reduction : By preventing the production and shipment of defective plastic bottles, AI-based vision inspection systems can drastically reduce costs related to returns, rework, and product recalls. Moreover, they help reduce material wastage by identifying defects early in the process.
Why the Packaging Industry Needs AI-Based Vision Systems?
As the packaging industry becomes increasingly competitive, it is critical for organisations to rationalize on costs. Artificial intelligence on the shop floor can be a key differentiator that not only helps maintain product quality but also maximises efficiency. The adoption of AI-based vision inspection systems provides a clear competitive edge by enhancing the accuracy and speed of quality control processes. These systems ensure that manufacturers can meet high industry standards while keeping costs under control.
If you’re in the plastic bottle manufacturing business and looking to optimize your production line, implementing an AI-based vision inspection system is a wise investment. Not only will it improve the quality and consistency of your products, but it will also streamline your operations and support long-term sustainability.
Conclusion
Plastic bottle defects are an ongoing challenge in packaging, but AI-based vision inspection systems offer a powerful solution to address this issue. By automating the detection of defects, ensuring real-time quality control, and reducing waste, these advanced systems can help manufacturers deliver higher-quality products with greater efficiency. Embrace AI in your production process today and watch your packaging operations reach new levels of precision and excellence.
For more information on how vision inspection systems can benefit your shopfloor, contact us today at info@factree.ai
Industries
© 2024. All rights reserved.