Automating Inspection of Injection Molded Components
Shreyas Rao
12/5/20245 min read
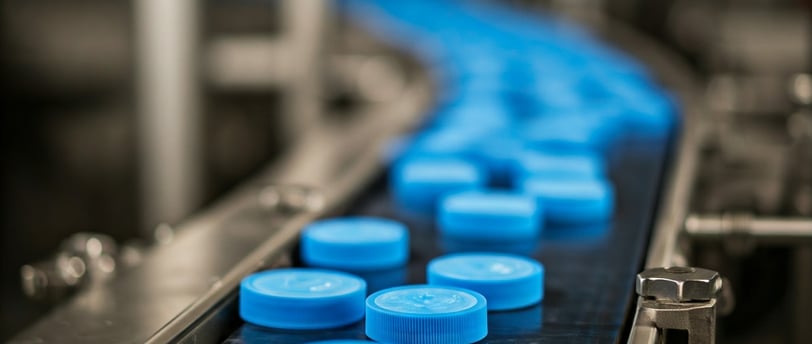
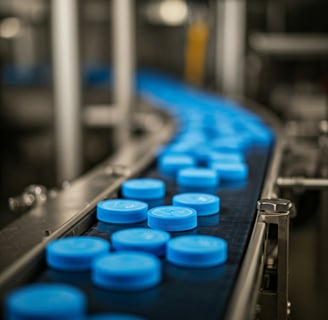
Plastic injection molding is one of the most widely used manufacturing processes for producing high-precision plastic components at scale. From automotive parts and medical devices to consumer electronics and packaging, the applications of injection-molded plastic components are vast and varied. Given the complexity and high-speed nature of injection molding, ensuring product quality is a significant challenge. This is where vision systems—sophisticated, non-contact inspection technologies—have become game-changers in the industry.
Vision systems equipped with high-resolution cameras and advanced image processing algorithms can rapidly inspect, measure, and verify molded parts with unparalleled accuracy. These systems provide manufacturers with real-time feedback on product quality, ensuring that defects are identified and corrected before the parts move further down the production line. Here’s a look at the most common use-cases for vision systems in plastic injection molding and the benefits they bring to the manufacturing process.
Key Use-Cases of Vision Systems in Plastic Injection Molding
Part Inspection for Surface Defects : One of the most critical applications of vision systems in injection molding is detecting surface defects on molded parts. Common defects include cracks, scratches, burn marks, sink marks, and flash (excess plastic around the edges of the part). Using high-resolution cameras, vision systems can identify these defects by analyzing the surface texture, color, and geometry of the molded part.
Vision systems can inspect parts at high speeds and with great precision, significantly reducing the likelihood of defective products reaching customers. By detecting defects early in the production cycle, manufacturers can avoid costly downstream corrections and maintain a high level of product quality.
Dimensional and Geometrical Measurement : Injection-molded parts often need to meet very specific dimensional tolerances, especially when used in industries like automotive or medical devices. Vision systems are ideal for non-contact dimensional measurement, allowing for the precise checking of critical features such as hole diameters, wall thickness, length, and overall shape. These systems use optical technology to take measurements with micron-level accuracy, ensuring that the parts fit within the required tolerances.
Automated vision systems also eliminate the need for manual measurement tools, reducing human error and the risk of miscalculation. In high-volume production, vision systems can inspect hundreds or thousands of parts per hour, making them essential for maintaining consistent quality across large batches.
Position and Orientation Verification: Many injection-molded parts require assembly or integration with other components. Vision systems can verify the position and orientation of each part, ensuring that it aligns correctly with other components in an assembly line. This is particularly crucial for complex parts with intricate features, where even a slight misalignment could affect the performance or functionality of the final product.
For example, in automotive manufacturing, plastic parts may need to be precisely positioned before they are attached to other assemblies. Vision systems can guide robotic arms or automated machinery to correctly orient and place parts, eliminating manual intervention and improving production efficiency.
Color and Marking Verification : Injection-molded parts are often required to have consistent coloring and markings, whether for aesthetic reasons or for identification purposes (e.g., logos, serial numbers, or barcodes). Vision systems can check for color consistency across large batches of parts, ensuring that the color of each component matches the specified standard. Additionally, vision systems can inspect markings or labels on parts, such as embossed logos, product information, or barcodes, to verify that they are correctly applied, legible, and free from defects. This is especially important in industries like packaging and medical devices, where proper labeling and identification are crucial for traceability and safety.
Flash Detection : Flash occurs when excess material leaks from the mold cavity during the injection process, forming unwanted protrusions or seams along the edges of a part. Flash detection is a critical use-case for vision systems in injection molding, as it ensures that such defects are identified and removed before the part moves forward in the production process. Vision systems can quickly identify even the smallest instances of flash by analyzing the edges of the part for irregularities. Once detected, the system can alert operators or trigger automated removal systems, improving both product quality and operational efficiency.
Detection of Incomplete or Overfilled Parts : Injection molding requires precise control over the amount of material injected into the mold. Overfilling can lead to excess material, while underfilling can result in incomplete parts. Vision systems are adept at inspecting the fill level and completeness of each molded part, ensuring that they meet the required specifications.
By using machine vision to detect inconsistencies in the molding process, manufacturers can avoid producing substandard parts, reduce material waste, and maintain consistent quality across production runs.
Assembly Verification : In some applications, plastic parts undergo secondary operations like assembly or welding. Vision systems can verify that parts are correctly assembled, ensuring that all components are in place and properly oriented. For example, in the production of automotive parts, a vision system might inspect whether clips, seals, or other parts have been correctly attached to the main molded component.
Benefits of Vision Systems in Plastic Injection Molding
The use of vision systems in plastic injection molding offers numerous benefits that contribute to higher quality, reduced costs, and improved efficiency.
1. Non-Contact Inspection
One of the biggest advantages of vision systems is that they perform inspections without making physical contact with the molded parts. This is especially valuable in injection molding, where delicate or fragile parts can be damaged by touch. By using optical technology, vision systems can inspect parts at high speeds without risk of contamination or damage, making them ideal for maintaining product integrity.
2. Increased Accuracy and Precision
Vision systems are incredibly precise, capable of detecting even the smallest defects or dimensional discrepancies. Unlike manual inspection, which can be prone to human error, vision systems provide consistent and accurate results every time. This level of precision is essential in industries where tolerances are tight, such as automotive or medical device manufacturing.
3. Higher Efficiency and Faster Throughput
With the ability to inspect parts at high speeds, vision systems significantly increase the efficiency of the injection molding process. This reduces downtime and speeds up production cycles, allowing manufacturers to achieve higher throughput without compromising quality. Vision systems can also operate continuously without fatigue, providing 24/7 quality control and reducing the need for manual inspection, which can be slow and labor-intensive.
4. Cost Savings
While the initial investment in vision systems can be significant, the long-term savings are substantial. By automating the inspection process, manufacturers can reduce labor costs, minimize scrap rates, and avoid costly product recalls. Moreover, the ability to identify defects early in the production process helps prevent costly downstream corrections and ensures that only high-quality products make it to the market.
5. Enhanced Traceability and Data Collection
Vision systems generate detailed inspection data that can be used for traceability, process optimization, and continuous improvement. These systems provide manufacturers with valuable insights into production trends, defect patterns, and areas for improvement. This data is crucial for compliance with industry regulations and quality certifications, and it helps manufacturers maintain high standards of product quality.
Conclusion
Vision systems are revolutionising the plastic injection molding process by offering precise, non-contact inspections that enhance product quality, reduce costs, and increase production efficiency. With applications ranging from surface defect detection and dimensional measurements to assembly verification and color consistency checks, vision systems provide manufacturers with the tools they need to maintain high-quality standards across the entire production cycle. As injection molding continues to evolve, the role of machine vision technology in driving productivity, reducing errors, and ensuring quality will only grow, making it an essential part of the modern manufacturing landscape.
For more information on how vision inspection systems can optimize your production, contact us today at info@factree.ai
Industries
© 2024. All rights reserved.